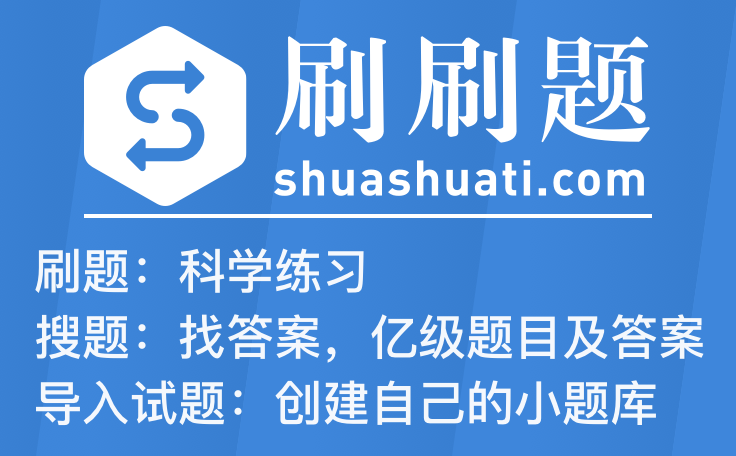
Dibble is formed of two autonomous divisions, Timber and Steel, and manufactures components for use in the construction industry. Dibble has always absorbed production overheads to the cost of each product on the basis of machine hours. Timber Division Timber Division manufactures timber frames used to support the roofs of new houses. The timber, which is purchased pre-cut to the correct length, is assembled into the finished frame. by a factory worker who fastens the components together. Timber Division manufactures six standard sizes of frame. which is sufficient for use in most newly built houses. Steel Division Steel Division manufactures steel frames and roof supports for use in small commercial buildings such as shops and restaurants. There is a large range of products, and many customers also specify bespoke designs for short production runs or one-off building projects. Steel is cut and drilled using the division’s own programmable computer aided manufacturing machinery (CAM), and is bolted together or welded by hand. Steel Division’s strategy is to produce novel bespoke products at a price comparable to the simpler and more conventional products offered by its competitors. For example, many of Steel Division’s customers choose to have steel covered in one of a wide variety of coloured paints and other protective coatings at the end of the production process. This is performed off-site by a subcontractor, after which the product is returned to Steel Division for despatch to the customer. Customers are charged the subcontractor’s cost plus a 10% mark up for choosing this option. The board of Steel Division has admitted that this pricing structure may be too simplistic, and that it is unsure of the overall profitability of sales of some groups of products or sectors of the market. Recently, several customers have complained that incorrectly applied paint has flaked off the steel after only a few months’ use. More seriously, a fast food restaurant has commenced litigation with Dibble after it had to close for a week while steel roof frames supplied by Steel Division were repainted. Following this, the production manager has proposed increasing the number of staff inspecting the quality of coating on the frames, and purchasing expensive imaging machinery to make inspection more efficient. The chief executive officer (CEO) at Dibble has approached you as a performance management expert for your advice. ‘At a conference recently’, he told you, ‘I watched a presentation by a CEO at a similar business to ours talking about the advantages and disadvantages of using activity based costing (ABC) and how over several years the adoption of activity based management (ABM) had helped them to improve both strategic and operational performance.’ ‘I don’t want you to do any detailed calculations at this stage, but I’d like to know more about ABC and ABM, and know whether they would be useful for Dibble’, he said. You are provided with extracts of the most recent management accounts for Timber and Steel Divisions: Required: (a) (i) Advise the CEO how activity based costing could be implemented. (4 marks) (ii) Assess whether it may be more appropriate to use activity based costing in Timber and Steel Divisions than the costing basis currently used. (8 marks) (b) Advise the CEO how activity based management could be used to improve business performance in Dibble. (13 marks)